Are you contemplating a transformative upgrade for your commercial space through the addition of concrete coatings? Whether you’re envisioning a sleek design, heightened functionality, or durable flooring, understanding each step of the process is crucial. In this in-depth guide, we’ll take you through the intricacies of the concrete coating journey, from consultation to the final stages of perfection.
- Consultation and Assessment: Crafting a Tailored Solution
- Obtain Your Quote: Fine-Tuning the Details
- The Concrete Coating Project Begins: Crafting Excellence
- The Concrete Coating Project Unveiled: Precision in Every Layer
- Crafting Excellence: Navigating the Concrete Coating Journey with Precision
- Conclusion: Crafting Commercial Spaces of Distinction
Consultation and Assessment: Crafting a tailored Solution
Embarking on the concrete coating journey begins with a detailed consultation with your seasoned floor improvement specialists. This initial meeting involves a conversation about your space’s unique needs, an assessment of current conditions, and an open dialogue to address any questions or concerns. By fully understanding factors such as your business type, design preferences, and existing floor conditions, our specialists can tailor their flooring recommendations precisely to meet your distinct needs.
Obtain Your Quote: Fine-Tuning The Details
After the assessment, your floor improvement specialist compiles a detailed quote, providing a detailed document outlining project specifics. This includes square footage, removal procedures, potential repairs, and selected products. A collaborative review of the quote ensures clarity, with adjustments made to align with your vision. Upon your satisfaction with the quote, your specialist will work with you to schedule your concrete floor coating installation at your convenience.
The Concrete Coating Project Begins: Crafting Excellence
Preparation: The Crucial Foundation
The foundation of any successful concrete coating project lies in meticulous preparation. Our flooring crew initiates this process by removing existing flooring. The crew will utilize diamond grinders to eliminate impurities, and potentially shot blast the floors for optimal adhesion. This meticulous process creates a pristine canvas, ensuring that your concrete is primed and ready for the coating application.
The Power of Diamond Grinders: Unveiling The Process
Diamond grinders boast industrial-grade diamond-embedded segments on their grinding discs. Spinning rapidly, these discs make contact with the concrete surface, efficiently removing imperfections, contaminants, and existing coatings; allowing a smooth canvas to emerge. This transformative process sets the stage for the subsequent coating application, ensuring not only functionality but also an excellence-defining aesthetic appeal.
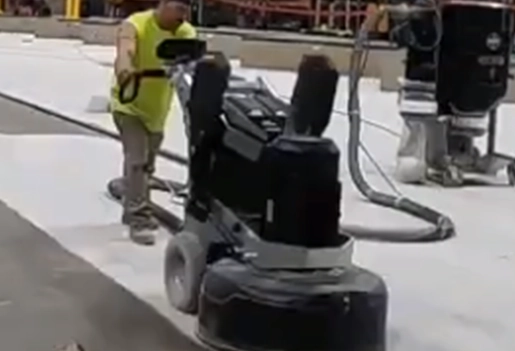
The process unfolds in two crucial steps:
- Removal of Existing Coatings: The magic begins with the effective stripping away of any existing coatings, adhesives, or sealers on the concrete surface, preparing the substrate for the forthcoming coating.
- Smoothing Out Imperfections: Uneven surfaces, bumps, and ridges are smoothed out during the grinding process, creating a level foundation for the coating application.
Transition to Shot Blasting: Perfecting the Canvas
The spotlight now turns to shot blasting, a dynamic and efficient technique that complements the artistry of diamond grinding. Just as diamond grinders create a foundation of perfection, shot blasting adds its unique touch to the canvas, preparing it for the next layers of coating. This process involves propelling small, high-velocity steel shots at the concrete surface, creating a thorough and uniform impact.
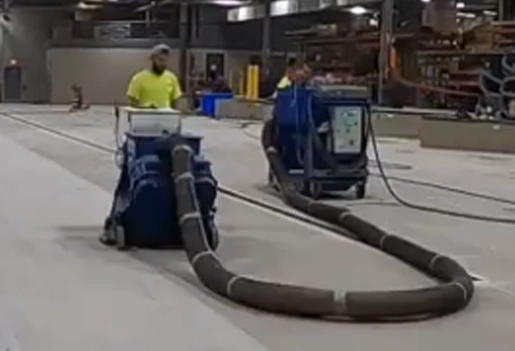
Purpose of Shot Blasting:
Removing Contaminants: Shot blasting efficiently eliminates contaminants such as dirt, grease, oil, coatings, adhesives, and other impurities residing on the concrete surface. This meticulous cleaning process is the cornerstone for optimal adhesion of the coating material.
Profiling the Surface: High-velocity steel shots impact the surface during shot blasting, creating a textured profile on the concrete. This profile isn’t just a visual enhancement; it’s a strategic move to enhance the bonding capacity of the coating, providing a surface primed for superior adhesion.
Exposing Aggregate (Optional): For those seeking an extra layer of aesthetic appeal, shot blasting can go beyond surface preparation. It can expose the aggregate within the concrete, offering a visually striking finish. In decorative or polished concrete applications, people often desire this feature.
Preparing for Repairs: Shot blasting goes beyond cleaning; it readies the concrete surface for repairs by opening up pores and creating a receptive substrate. This ensures that subsequent patching or filling of cracks and imperfections adheres seamlessly, fortifying the structural integrity of the coated concrete.
A Dynamic Duo Unleashed:
Essentially, the combined prowess of diamond grinding and shot blasting creates a dynamic duo. These two systems ensure the concrete substrate is not only pristine but also optimally prepared for the subsequent coating application. These techniques, each with its unique strengths, work in tandem to lay the foundation for durable, visually appealing, and long-lasting coated concrete surfaces.
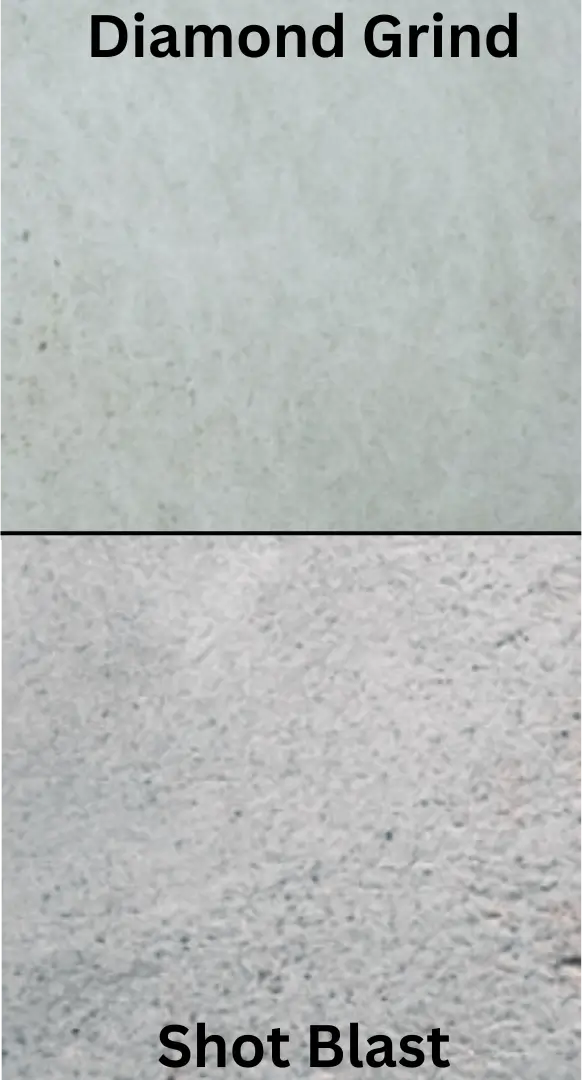
The Concrete Coating Project Unveiled: Precision in Every Layer
Repair: Addressing Concrete Imperfections
Before the unfolding of the coating process, our focus turns to addressing any imperfections within the concrete surface. Despite its durability, concrete is not immune to wear and tear, and cracks may emerge over time due to various factors. Addressing them is crucial for the longevity and aesthetics of your coated concrete floor.
Crack Identification and Repair:
Routing and Cleaning: The crack repair process commences with the widening and cleaning of cracks using specialized tools like grinders or routers. This step creates an optimal groove for the repair material to bond effectively.
Crack Filling: Epoxy or polyurethane-based crack fillers, renowned for their bonding strength, are meticulously applied to fill and seal the cracks. This not only prevents further propagation of cracks but also establishes a resilient bond with the existing concrete.
Spall and Surface Repair:
Removal of Damaged Concrete: Spalled or damaged areas are carefully removed to expose sound concrete. This process involves chipping away loose or damaged portions until solid, unaffected concrete is revealed.
Surface Cleaning: The repaired area undergoes thorough cleaning to eliminate dust, debris, and contaminants, ensuring optimal adhesion of the repair material.
Application of Repair Mortar or Patch: A high-quality repair mortar or patch material is then applied to the prepared surface. This material bonds seamlessly with the existing concrete, restoring strength and integrity.
Joint Repairs: Protecting Vulnerable Points
Expansion joints and control joints are critical elements in concrete structures, and maintaining their integrity is paramount. Our process includes meticulous cleaning and sealing of these joints to prevent water infiltration, ensuring the long-term durability of your coated concrete surface.
Surface Cleaning: Preparing for Perfection
Dust and Debris Removal: Before the coating application, the entire surface undergoes a meticulous cleaning process to remove any residual dust, debris, or contaminants from the grinding and repair processes. This step guarantees an unblemished canvas for the upcoming phases.
Application of Bonding Agents (Optional): In some cases, a bonding primer may be applied to enhance the adhesion between the repaired concrete surface and the coating. This step is particularly beneficial, especially for aged or porous concrete.
Final Inspection: Ensuring Excellence
During a final inspection, experts validate the seamless execution of all repairs and confirm that the surface is primed for the coating. This meticulous attention to detail ensures that your concrete coating project builds on a foundation of excellence, promising not just aesthetics but enduring functionality.

Crafting Excellence Navigating the Concrete Coating Journey with Precision
Embarking on the concrete coating journey involves a meticulous orchestration of techniques. Each contributes to the creation of a durable and visually appealing surface. Let’s delve into the intricacies of the coating process to explore the nuanced timing of screed and power trowel applications, along with an expanded understanding of primer and build coats.
The Crucial Role of Primer in Concrete Coating
In the intricate process of concrete coating, the primer stands as a foundational element, playing a pivotal role in ensuring the success and longevity of the entire coating system. The purpose of the primer extends beyond being merely the initial layer; it serves as a crucial preparatory agent, enhancing adhesion, sealing the floor, and fortifying the concrete substrate.
Surface Sealing and Hardening: One of the primary functions of the primer is to seal the concrete surface effectively. By penetrating the pores of the concrete, the primer creates a protective barrier that seals the floor, preventing moisture absorption and enhancing overall durability. Additionally, the primer contributes to the hardening of the concrete beneath, creating a robust foundation for subsequent coating layers.
Enhancing Adhesion: Adhesion is a critical factor in the success of any coating system. The primer acts as a bonding agent, deeply penetrating the concrete substrate and creating a surface to which subsequent coatings can adhere strongly. This enhanced adhesion ensures that the entire coating system remains securely bonded to the concrete, preventing issues such as peeling or bubbling.
Creating a Base Layer: Beyond its sealing and bonding properties, the primer acts as the foundational base layer for the build coats that follow. It provides a stable and consistent surface on which subsequent layers of coating can adhere and form a cohesive structure. This layered approach contributes to the overall resilience and longevity of the coated concrete floor.
Improved Chemical Resistance: Depending on the specific formulation, primers often include additives that enhance chemical resistance. In environments where the coated concrete may face exposure to chemicals, oils, or other potentially damaging substances, this proves particularly beneficial. The primer acts as a protective shield, mitigating the impact of chemical exposure and preserving the integrity of the coating.
Compatibility with Subsequent Coatings: The primer is carefully selected to ensure compatibility with the subsequent build coats and topcoats. Achieving a seamless and integrated coating system that performs optimally over time crucially depends on this compatibility. The primer acts as a bridge, facilitating the smooth transition from one layer to the next.
In essence, the primer is not just a preliminary layer in the concrete coating process; it is a strategic and essential component that sets the stage for the entire system. Its contributions to adhesion, sealing, and overall durability make it a cornerstone in crafting coated concrete surfaces that stand the test of time.
Purpose of Screed in Concrete Coating
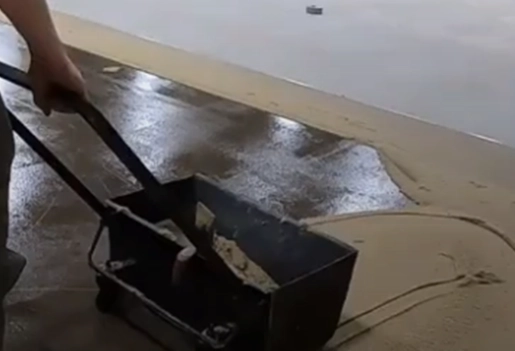
The purpose of screed in concrete coating is to create a level and smooth surface on which the coating can be applied. Screeding is a crucial step in the preparation of the concrete substrate, and it serves several key purposes:
Surface Leveling: Screeding helps to level out any unevenness, bumps, or imperfections in the concrete surface.
Thickness Control: Screeding allows for precise control over the thickness of the coating application. Achieving a uniform thickness is essential for the coating to perform optimally and to meet the project specifications.
Enhanced Adhesion: A properly screeded surface provides better adhesion for the coating material. It eliminates high and low spots, allowing the coating to bond more effectively with the substrate.
Improved Aesthetics: By creating a level surface, screeding contributes to the overall aesthetics of the coated concrete. It ensures a visually pleasing and professional finish.
By incorporating screeding into the concrete coating process, the substrate is prepared to receive the coating most effectively. A well-screeded surface contributes to the longevity, performance, and visual appeal of the final coated concrete.
Precision and Polishing: Unveiling the Purpose of Power Trowel in Concrete Coating
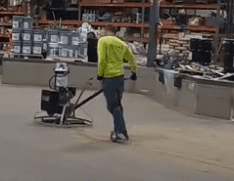
In the meticulous journey of concrete coatings, the power trowel emerges as a versatile tool, bringing forth its unique capabilities to refine and perfect the coated surface. Its purpose extends beyond mere application, diving into the realms of precision, smoothing, and ultimately contributing to the aesthetic and functional excellence of the final coated concrete floor.
In essence, the power trowel serves as the concluding artist’s brushstroke in the concrete coating process. Its purpose transcends the functional aspects of leveling and smoothing; it delves into the realm of craftsmanship, adding finesse to the coated surface. As it glides across the concrete, the power trowel transforms the utilitarian into the extraordinary, creating a surface that not only performs with durability but also captivates with its polished elegance.
Build Coats: Tailoring Thickness for Durability
Build coats play a crucial role in the concrete coating process, serving multiple purposes to enhance the overall durability, aesthetics, and performance of the coated surface. Here are the primary purposes of build coats in concrete coating:
Optimizing Adhesion for Topcoats: The build coats serve as an intermediate layer that optimizes adhesion for the application of topcoats. A well-prepared substrate, achieved through the build coats, ensures that the topcoats bond effectively with the underlying layers, creating a cohesive and durable coating system.
In summary, build coats are a fundamental component of the concrete coating process, providing thickness, strength, wear resistance, aesthetics, and a well-prepared substrate for subsequent coating layers. Their strategic application contributes to the overall success of the coating system in commercial and industrial settings.
Topcoat in Concrete Coating: Enhancing Protection and Aesthetics
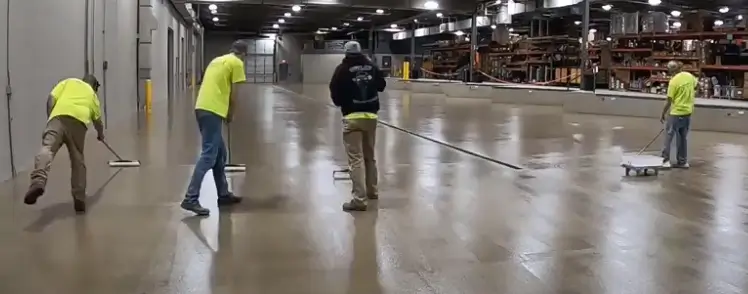
Purpose of Topcoat: The topcoat in concrete coatings serves as the final layer that provides a range of benefits to enhance the overall performance, durability, and aesthetics of the coated surface. The key benefits of applying a topcoat include:
In conclusion, the topcoat is the final layer that adds a protective and aesthetic finishing touch to concrete coatings. Its application is a critical step in ensuring the longevity and performance of the coated surface in diverse settings.
Sealing Edges: Protecting Vulnerable Points
Sealing edges during the concrete coating process is a critical step to prevent debris infiltration, enhance the overall appearance, and prolong the life of the coated surface. The edges where the floor meets the wall are vulnerable points where dirt, moisture, and debris can accumulate, leading to potential damage to the coating over time.
Importance of Sealing Edges
Preventing Moisture Intrusion:Sealed edges act as a deterrent to moisture intrusion, which is essential in environments where water exposure is a concern. Moisture can lead to various issues, including coating delamination, mold growth, and structural damage.
By following a meticulous process to seal edges during the concrete coating application, the risk of debris infiltration is significantly reduced. This, in turn, contributes to the overall durability, aesthetics, and performance of the coated concrete surface.
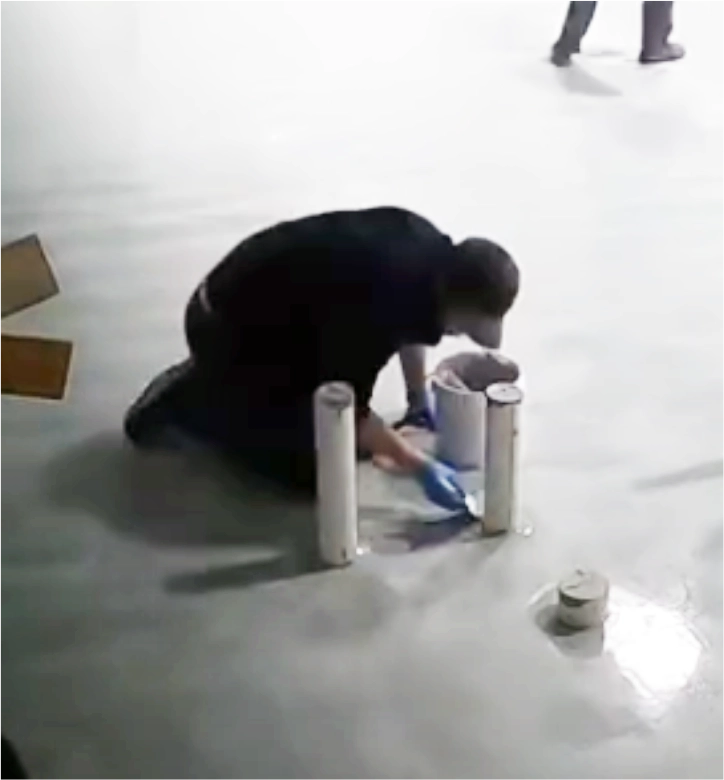
Conclusion: Crafting Commercial Spaces of Distinction
Undoubtedly, any business faces a significant decision when investing in new or upgraded floors. To ease any concerns, we encourage you to reach out to a Floor Improvement Specialist today. Schedule your consultation, obtain a personalized quote, and then bear witness to the transformation of your commercial space with concrete floor coatings customized for you.
Experience the Excellence of Advantage Coating – Your Trusted Concrete Coating Partner!